| 7/10/13 I noticed it has been a while since I last posted to my blog. Things are going well, and I have been keeping busy making pieces to sell, including some spiral chip-and-dip servers. I'm experimenting with a few glaze combinations on some of the flower vases, using them as "test tiles" to see what can be combined to make something even more interesting for colors and glaze effects. I'm even experimenting with making some flower "tubes", so hopefully I'll have a new product to sell shortly once it has gone through a few "upgrades". Tomorrow's show in Rochester should be fun, as I have several customers coming to pick up pieces they ordered, and I get to "brainstorm" with another customer using an older piece I made with my sister a few years ago. |
1 comment | Post comment
 | I think here is the best list of pottery items that everyone should make. https://www.bestcrafterstudio.com/pottery-that-sells-well/ | -- Sarah, 9/23/22
|
|
6/24/12It seems there is plenty to do lately trying to make enough pieces for the shows. Here some flower vases and wine chillers are cooling on a rack after coming out of the kiln. I like to carve some wine-related designs into the wine chillers. I am planning to make more platters, and variety of other items to allow customers some nice choices from which to pick. Off to the studio! :) |
Be the first to post a comment.
|
6/13/12 Crazy windy at this past weekend's show in Mankato. I managed to lose 10 pots to the wind. One was blown off my table and somehow managed to break on a display holder. The other nine bit the dust when a couple of nasty gusts of wind toppled one of my racks. Ouch! It wasn't all bad news though, as I did managed to win 2nd place at the event. Yay! Now back to the studio to make replacements for some of the smashed pieces. Go Go GOOOOO! |
Be the first to post a comment.
|
6/11/12 I installed a new kiln earlier this year so that I can use an electronic controller to fire the kiln (rather than manual switches). I'm still working on getting the bugs out, as the kiln appears to like to over-fire my pieces. I found a loose screw and also changed out the thermocouple, but even with those changes, I'm seeing a one cone overfiring. I made an aluminum movable rack on which to set the kiln base, allowing me to move the kiln around in the studio when needed. I've organized the kiln shelves and posts on a wire rack to make it easier to load and unload the kilns. Time to head back to the studio and get more things made for the upcoming shows. Have fun! :D |
Be the first to post a comment.
|
10/26/11 I've been busy in the studio trying to keep up with producing enough for all the sales on my schedule. Somehow I managed to find the time to take a few photos during the rush. I like to write the serial number on the bottom of the piece using marker so that I can read it more easily after doing the waxing process. I try to record all the glazes used on each piece in a log book so that I can reference it at a later time. That's helpful in recreating a glaze combination that works especially well. :) I'm enjoying the extra twists and turns I'm putting on my chip-n-dips, which lets me be artistically expressive, but still allows for a functional piece. I am hoping that people will find them to interesting and fun to use. |
Be the first to post a comment.
|
9/6/11Making a few mugs lately to add to the items for sale, so I pulled a number of handles from which to select and attach. I'm very happy with the various shapes and sizes of the mugs... some of them are very unique... interesting... distorted even! (Chuckles) If everthing goes well, I am hoping to do another bisque firing, get things glazed, and do a glaze firing by Thursday evening so that things have time to cool down Friday and are available for Saturday's sale. |
Be the first to post a comment.
|
7/25/11 With my class reunion out of the way this past weekend, I've been busy trying to get things ready for an exciting two-day local show. Got some interesting pieces I've made lately, so I'm excited to see what I do in the glazing arena for them once they have been bisque fired. I need to be careful with my experimentation so that I have some decent pieces for the show, of course! I've added a few platters to my inventory recently, so now I'd like to get some bowls and other slab shapes made to help round out my presentation. The large items generally get the "Wow" factor, so have been working on making some fairly large pieces. Besides, they are more fun to work on too! :D Carving takes time, but the results are so enjoyable. I'll have to be careful to price these recent ones correctly to take into the account the time I've spent carving and designing them. Tomorrow I'm planning to take apart my primary kiln to do some work on it, and then get it assembled again for a firing tomorrow night. Got to get some pots glazed and fired!!!! |
Be the first to post a comment.
|
7/12/11I've been trying to focus a little more on exploring my platters, and to see what various things I can do to design and decorate them... and with every step forward, it feels more and more like I'm just starting to scratch the surface (pun pun) of what can be done. The spiral rolling stamp design seems pretty popular, so I may work on making a few more rolling stamps to use, as I've only made three rolling stamps and one cylinder stamp so far. I would like to have ten stamps from which to choose eventually (or more if I get real ambitious). I'm starting to use some other colors for clay, including a Raku clay body that I used to make another wine chiller. You can see in the photo that I've carved the wine glass, and have yet to add the grape bunch. I'm not yet sure if I'll fire this piece in the Raku kiln, or just fire it along with my other stoneware in the electric kiln. Will have to see what time permits. Mixing several types of clay also has been yielding some interesting pieces, although it also can give its own set of problems for drying and clay shrinkage rates. I like the swirl effect when throwing the verigated clay on the wheel. But still have to be careful to avoid the stresses and cracking that can happen more easily when using two different clay bodies, as seen on the platter. Ouch! Looks like that one is headed for the scrap heap. Guess they can't all be winners... LOL. Have a fantastic day, everyone! Carl |
Be the first to post a comment.
|
7/1/11Just started the kiln and it is nearly 2AM. I'll have to set a timer to wake me up to turn it up every 1.5 hours. Some of the glazed pieces would not fit in this smaller kiln, so they will wait to be fired in the next glaze load. Looks like a busy weekend, with the farmer's market sale in the morning, and a two-day sale on Sunday/Monday. Take care and Happy Fourth! Carl |
Be the first to post a comment.
|
6/21/11It seems there is not enough hours in the day to do everything one would like to accomplish. Ha ha. Here are a couple of recent photos of pottery in progress in my studio. The platters, once thrown and decorated, need to dry for some time before they can be flipped to add the serial number and signature. I use cloths to control the speed of the drying so that they dry more evenly to avoid warpage. Normally I avoid production pottery, trying to impart each piece with a style/soul all its own. I've since rethought that philosophy in regards to the Asian vases, since I make so many of them. I still vary the glazing on them so that one could still call them all unique, but as you see in this photo, I'm starting to make more of them at a time for efficiency's sake. 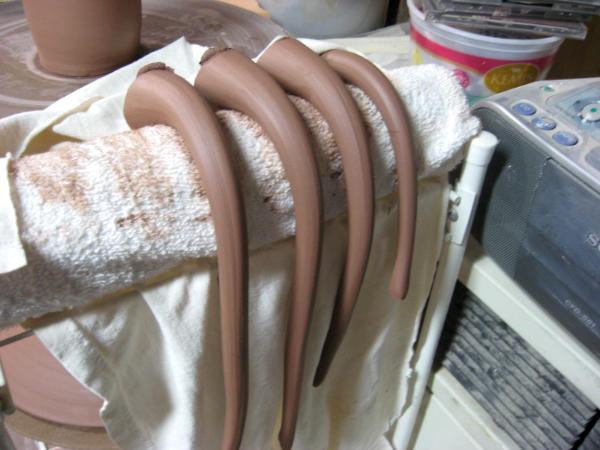 |
I pulled some handles for a few pitchers I made. The photo shows them resting to stiffen up before being attached to the pots. Pulling the handles takes a bit of time, but I think the feel of the results is worth the effort. I think the pulled handle feels more natural and comfortable to use than the standard flat slab handle. Personal preference, of course. :D Time to get back to the studio. I have a glaze kiln firing now. I was told by the power company that they would like to shut off the power one pole down to make a repair there in a few hours. Of course, they tell me this after I've already fired up my kiln. Ouch! So I'm not sure how much it will affect the load... am hoping that when the power comes back on, that it will catch back up and still fire the glazes correctly. I'm glad I put a cone pack in the kiln when I loaded it... it might help me tell what is happening in this unusual firing. Carl |
Be the first to post a comment.
| Previously published: |